The Intricate World of Plastic Injection Molds
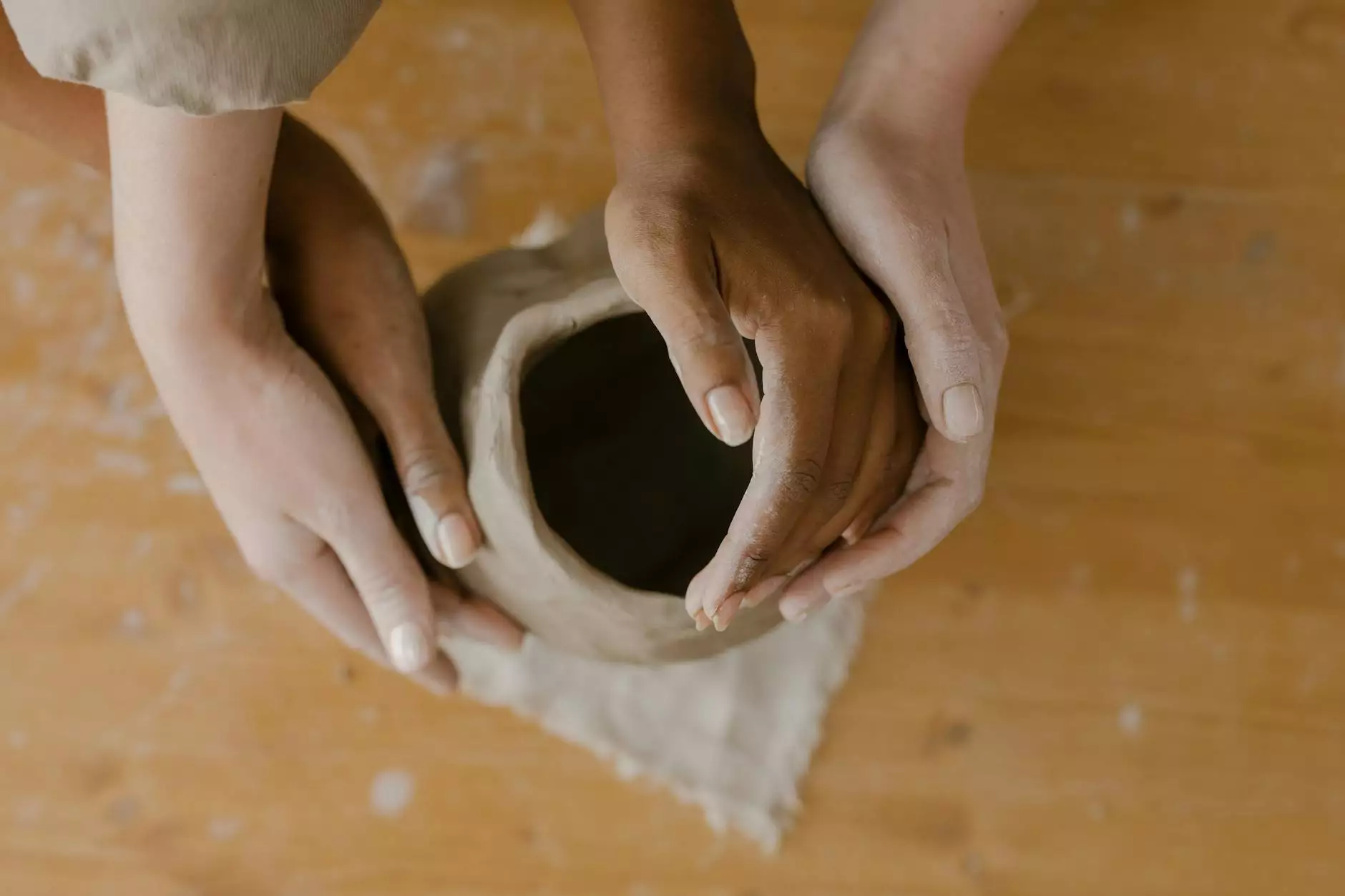
In the rapidly evolving landscape of manufacturing, plastic injection molds stand out as a cornerstone of production efficiency and innovation. This article delves deep into the mechanics, benefits, and applications of plastic injection molding, highlighting why it has become indispensable for industries worldwide.
Understanding Plastic Injection Molding
Plastic injection molding is a manufacturing process used to produce parts by injecting molten material into a mold. This technique is widely preferred in the production of plastic parts due to its ability to create highly complex shapes with precision and consistency.
How Plastic Injection Molding Works
- Design Phase: It all starts with a detailed design of the component, employing CAD software to visualize and plan the mold and finished product.
- Fabrication of the Mold: Skilled engineers then create a metal mold tailored to the design specifications to withstand high pressures and temperatures.
- Injection Process: Molten plastic is injected into the mold, where it cools and solidifies into the desired shape.
- Demolding and Finishing: Once cooled, the mold opens, and the finished product is ejected. Post-processing may occur, including trimming, painting, or assembling.
Benefits of Plastic Injection Molding
The plastic injection molding process offers numerous advantages. Below are some key benefits that explain why this method is favored in manufacturing:
- High Efficiency and Speed: The cycle time for injection molding is significantly lower compared to other manufacturing methods, allowing for mass production of components in a shorter time.
- Cost-effectiveness: While the initial mold creation may be costly, the high volume of production can significantly reduce the cost per unit.
- Material Versatility: A variety of plastics can be used in injection molding, enabling manufacturers to choose materials that best fit the functional and aesthetic requirements of their products.
- Complex Geometries: The ability to produce intricate designs with fine details is unparalleled in plastic injection mold technology.
- Consistency and Quality: The process ensures that each part produced maintains the same quality, dimension, and performance, greatly reducing waste and rework costs.
Applications of Plastic Injection Molding
Plastic injection molding finds applications in a wide range of industries, including:
1. Automotive Industry
From dashboard components to electrical enclosures, the automotive sector employs plastic injection molds to create lightweight, durable parts that improve fuel efficiency without sacrificing safety.
2. Consumer Electronics
Gadgets and devices require intricate components that often rely on injection molded parts. This includes casings, buttons, and internal structures that need to be moldable and resilient.
3. Medical Devices
In the medical field, precision is crucial. Plastic injection molding allows for the creation of custom syringes, connectors, and various prosthetics that meet stringent regulatory standards.
4. Packaging Industry
Injection molds are used to create everything from containers to closures, providing effective sealing and protection for products.
5. Home Goods and Appliances
Everyday items like storage containers, furniture components, and kitchenware are frequently made using plastic injection molding technology to meet consumer demand for affordability and style.
Choosing the Right Partner for Injection Molding
When seeking a provider for plastic injection mold manufacturing, consider these factors:
- Expertise: Look for companies that specialize in injection molding with a proven track record.
- Technology: The latest machinery and technologies can enhance precision and reduce production times.
- Quality Assurance: Ensure the partner has rigorous quality control processes to meet industry standards.
- Customer Support: A reliable partner should offer consistent support during and after production.
- Flexibility: The ability to adapt to design changes and manufacturing challenges is crucial.
Future Trends in Plastic Injection Molding
The plastic injection molding industry is poised for continued growth and evolution. Here are a few emerging trends to watch:
1. Industry 4.0 Integration
As manufacturing becomes increasingly digitized, the integration of IoT, AI, and data analytics in plastic injection molding processes is expected to enhance efficiency and predictive maintenance.
2. Sustainable Practices
With growing environmental concerns, manufacturers are focusing on sustainable practices, including the use of recycled materials and energy-efficient processes.
3. Customization and Rapid Prototyping
The demand for personalized products continues to rise. Advances in 3D printing and rapid prototyping will complement plastic injection molding, allowing for quicker adaptations to market needs.
4. Advanced Materials
Research into new polymers and composites will enable manufacturers to create even more durable and lightweight components, expanding the scope of applications.
Conclusion
Plastic injection molds represent a vital technology in modern manufacturing, driving efficiency, precision, and innovation across various industries. With its many benefits and broad applications, it is clear why businesses are investing in this technology to meet the demands of tomorrow's marketplace.
As DeepMould.net continues to lead in the field of plastic injection molding, companies looking for reliable and innovative solutions should consider partnering with us to leverage our expertise and advanced technologies.
For more detailed insights and tailored solutions, visit DeepMould.net, and take the first step towards enhancing your manufacturing capabilities with our superior plastic injection molding services.