Revolutionizing Manufacturing with Electric Injection Molding Machines
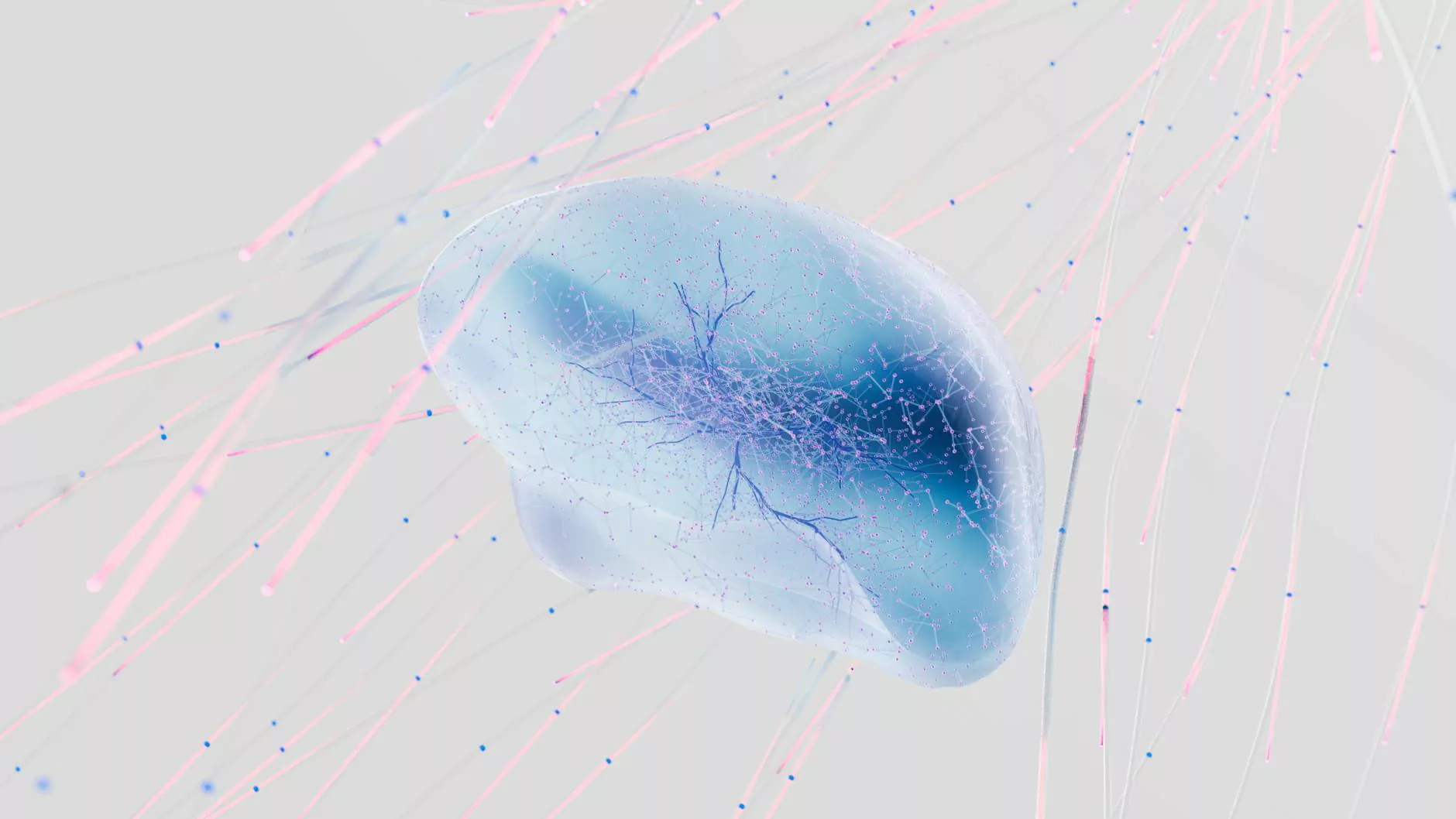
In today's fast-paced industrial environment, manufacturers are continually searching for ways to enhance productivity while maintaining high-quality standards. One of the most significant advancements in the realm of manufacturing technology is the electric injection molding machine. This innovative equipment is transforming how businesses approach production processes, particularly within the metal fabricators sector.
Understanding Electric Injection Molding: The Basics
To appreciate the impact of the electric injection molding machine, it's essential to understand what it is and how it functions. Unlike traditional hydraulic machines, electric molding machines use electric motors to drive all their operations. This fundamental difference influences various aspects of their operation, including energy consumption, precision, and speed.
Key Components of Electric Injection Molding Machines
- Electric Servo Motors: These motors deliver high precision and rapid response times, ensuring consistent quality in production.
- Control Systems: Advanced control systems enable real-time monitoring and automation of the injection molding process.
- Clamping Mechanisms: Electric machines utilize effective clamping systems to maintain part integrity and minimize defects.
- Temperature Control Units: Precise temperature regulation is vital for optimal molding, leading to enhanced product quality.
The Benefits of Electric Injection Molding Machines
The shift towards electric injection molding technology brings with it numerous benefits that can significantly influence a business's bottom line. Let's explore some of these advantages in detail:
1. Enhanced Energy Efficiency
One of the most significant advantages of using an electric injection molding machine is energy efficiency. Traditional hydraulic machines consume a considerable amount of energy, often leading to high operational costs. In contrast, electric machines can reduce energy consumption by up to 60% or more. This considerable reduction not only translates into cost savings but also aligns with global sustainability initiatives.
2. Superior Precision and Consistency
Precision is critical in manufacturing, particularly in the metal fabricators category. Electric injection molding machines offer a level of accuracy that is hard to achieve with hydraulic models. The servo motors used in these machines ensure that every injection is consistent, thus reducing scrap rates and enhancing the quality of final products.
3. Reduced Cycle Times
Speed is of the essence in manufacturing, and electric machines are designed to optimize cycle times. The rapid response of electric servo motors allows for quicker molding and cooling cycles, leading to increased productivity. Businesses can produce more parts in a shorter timeframe, which is crucial in meeting market demands.
4. Lower Operating Costs
With improved energy efficiency, reduced need for maintenance, and higher production rates, operating costs associated with electric injection molding machines are significantly lower compared to hydraulic options. This benefit is particularly compelling for companies looking to maximize their return on investment.
5. Environmentally Friendly Manufacturing
As industries strive to minimize their ecological footprint, the electric injection molding machine shines as a greener alternative. These machines produce less waste and utilize energy more efficiently, which is essential for companies committed to sustainable practices. Moreover, the reduced hydraulic fluids eliminate disposal and leak-related environmental concerns.
Applications of Electric Injection Molding Machines in Metal Fabrication
The versatility of electric injection molding machines has made them pivotal in various applications, particularly within the metal fabrication industry. Here are some prominent applications:
1. Production of Metal Components
Electric machines are highly effective in producing precision metal parts for various industries, including automotive, aerospace, and electronics. Their ability to maintain tight tolerances makes them ideal for components that must meet rigorous specifications.
2. Manufacturing of Complex Geometries
Modern electric injection molding machines are capable of manufacturing intricate shapes and designs that may be challenging for other molding methods. This capability opens the door to innovation and creativity, allowing businesses in the metal fabrication sector to explore new product designs and market opportunities.
3. Small-Batch Production Runs
The flexibility of electric molds makes them perfect for small to medium production runs. Manufacturers can quickly switch between different mold designs without significant downtime, catering to customized orders that are increasingly in demand.
Choosing the Right Electric Injection Molding Machine
When considering the integration of an electric injection molding machine into your operations, it's essential to evaluate various factors to determine the best fit for your business:
- Production Capacity: Analyze your expected output to choose a machine that can meet your volume requirements.
- Mold Compatibility: Ensure that the machine is compatible with the molds you plan to use, considering both size and complexity.
- Budget: Evaluate initial investment costs against long-term savings on energy and maintenance.
- Technology and Features: Look for advanced features like real-time monitoring and automation capabilities that can enhance productivity.
Success Stories: Companies Leveraging Electric Injection Molding Machines
Many businesses have successfully adopted electric injection molding machines to improve their manufacturing processes. Following are a few notable examples:
Case Study 1: Automotive Industry Leader
A major automotive manufacturer integrated electric injection molding machines into its operations to produce high-precision dashboard components. The transition resulted in a 25% reduction in production costs and improved the quality of components, which significantly enhanced customer satisfaction.
Case Study 2: Electronics Manufacturer
An electronics producer implemented electric molding technology for the fabrication of intricate connectors and components. By doing so, they were able to reduce cycle times by 30%, allowing them to meet tighter deadlines and grow their market share.
The Future of Electric Injection Molding Machines
As technologies continue to evolve, the future of electric injection molding machines looks promising. Innovations in automation, artificial intelligence, and machine learning are set to enhance the capabilities of these machines even further, allowing for smarter production processes that adapt to market needs.
Investing in Innovation
At DeepMould.net, we are committed to providing state-of-the-art electric injection molding solutions for the metal fabricators industry. With a focus on quality, innovation, and sustainability, we help businesses thrive in a competitive landscape. Our experienced team is ready to assist you in integrating these advanced machines into your operations.
Conclusion: Transforming the Manufacturing Landscape
The shift towards electric injection molding machines marks a significant change in the manufacturing sector, particularly for metal fabricators. By embracing this technology, companies can not only boost their operational efficiency and product quality but also make strides towards a more sustainable manufacturing future. With numerous benefits and a broad range of applications, the electric injection molding machine is undeniably integral to the evolution of modern manufacturing processes.
For businesses looking to stay ahead of the curve, investing in electric injection molding technology is a crucial step toward innovation, efficiency, and success.